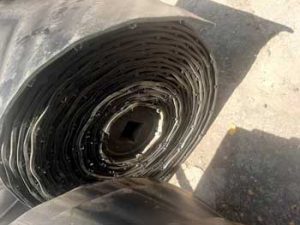
خرابی و فساد تسمه نقاله ها و تایر های لاستیکی-عوامل پوسیدگی لاستیک
خرابی و فساد تسمه نقاله لاستیک ها -فساد و خراب شدگی (Deterioration)
لاستیک در برخی شرایط سرویس دهی با کاربردهای مختلف برخورد می کند که خواص آن را با سرعتها و درجات مختلف خراب می کند. شرایط خرابی و فساد تسمه نقاله شامل :
- در معرض قرار گرفتن با هوا
- ازون
- تابش پرتو
- شعله و دماهای بالا و خیلی پایی
خرابی و فساد تسمه نقاله های لاستیکی
تعبیر خواص لاستیک در شرایط محیطی به طور قابل توجهی، متغیر است و به شرایط واقع شده بستگی دارد. در برخی موقعیتها، تابش شدید نور آفتاب و دماهای بالا به طور گسترده، تسمه نقاله لاستیکی را فاسد و خراب می کند. در برخی موارد دیگر، ازون ممکن است عامل اصلی فساد باشد. از جمله روشهای اصلی تستهای آزمایشگاهی برای اندازه گیری فساد و خرابی تسمه ها و شبیه سازی اثرات هوا تحت شرایط کنترل شده 750 ASTM D است.
دلیل خرابی لاستیک ها(هوا)
این آزمایش از یک نمونه کشیده شده یا آزاد استفاده می کند که در معرض نور فرابنفش قویتر از نور آفتاب قرار می گیرد. حتی می توان نوری شبیه به تابش آفتاب را در نظر گرفت. این شرایط، نمونه را خراب و فاسد می کند و عیوبی روی سطح نمونه بوجود می آورد که سبب کاهش طول گسیختگی و استحکام کششی می شود.
هنگام اجرای این آزمایش، برای خراب شدن یک نمونه مرجع بایستی برای حصول نتایج بیشتر و مفهوم تر بکار گرفته شود. برای ارزیابی کلی اثر شرایط جوی، نمونه ها اغلب، در شرایط آب و هوایی مختلف آزمایش می شوند.
دلیل فاسد شدن و خرابی تسمه و انواع لاستیک ها (ازون)
این گار ناپایدار عموما در اتمسفر در تمرکزهای به شدت پایین چندین قسمت در صد میلیون (pphm) تشکیل می شود حتی این تمرکز و غلتهای پایین می تواند سبب ترکهایی در لاستیک تحت تنش شود که با زاویه های قائمه نسبت به جهت تنش اعمالی شکل می گیرد.
امروزه، 78-ASTM D1149 تمرکزهای ازون را به صورت فشار جزئی اوزن بیان می کند، ترجیحا به صورت pphm بیان می شود، فشار جزیی استاندارد MPa 50 است. استفاده ار فشار جزیی ازون نوسانات فشار اتمسفریک را به حساب می آورد. بدترین شرایط تنها بالای سطح تنش بحرانی (حدود MPa 0.06 یا psi 8.7) رخ میدهد که متناسب با کرنش بحرانی حدود %3 است.
ترکهای مجزا عمیق و گسترده تنها بالای سطح تنش بحرانی تشکیل می شود و اینها در قیاس با ترکهای کوچک احتمالا، علت اصلی تر شکست محصول به حساب می آیند. افزایش تنش یا کرنش تشکیل ترکهای ریزتر و بیشتر را به همراه خواهد داشت. ترکهای ازون قادر نیستند به عمق خیلی زیادی در قطعات لاستیکی بزرگ نظیر : ياتاقانهای پل نفوذ کنند زیرا، آنها به مجرد پیدایش بیشتر تحت تنش فشاری یا تنش کششی قرار می گیرند.
بنابراین، ترک اوزن مشکل کم اهمیت تری در قطعات لاستیکی است که در فشار بکار برده می شوند. با این وجود، به لحاظ تجربی و عملی پسندیده است که از ترکهای ازون با استفاده از واکسهای محافظ یا انتی ازونها جلوگیری شود. زیرا، ترکهای ازون بد منظر هستند و می توانند خستگی را سبب شوند و رشد ترک سرانجام به گسیختگی محصول لاستیکی منتهی شود.
دلیل خرابی و پوسیدگی لاستیک ها ( تشعشع انرژی بالا)
لاستیکی که در راکتورها و زیردریاییهای هسته ای استفاده می شوند. نیازمند داشتن مقاومت در برابر تشعشع گاما هستند که می تواند سختی و مدول آنها را افزایش دهد. برای لاستیکی که در حین پرتودهی به طور کامل پیوندهای عرضی ایجاد می کند، تشعشع 100 مگاراد مقدار اصلي 100 – S را تقريبا، دو یا سه برابر می کند. 1672 ASTM D مقاومت پلیمرها را در برابر تشعشع انرژی بالا اندازه گیری می کند.
یک کابل مورد استفاده در صنایع هسته ای مثالی از یک محصول لاستیکی است که باید هم مقاومت در برابر تشعشع و هم مقاومت در برابر شعله را داشته باشد. خواص فیزیکی عایقی EPDM که در کابلها بکار برده می شود تنها بالاتر از 10 راد، اندکی تغییر می کند.
کابل هنگامی که با تستهای شعله افقی و عمودی مورد آزمایش قرار گرفت، خواص تأخیرانداز شعله خوبی از خود نشان داد. مقاومت سیم و کابل صنعتی در برابر حرارت هم خواستنی است. یک طرح آرهنيوس (Arrhenius plot) برای تولید و جمع آوری اصطلاحات مرتبط با خواص سیمهای خم شده در C° 150 بکار گرفته شد.
پوشش بر پایه الاستومرهای جدیدتر نظیر: EPDM, EVA ،CPEو TPE/TPV شدید جایگزین پوشش بر مبنای ترکیبات IIR ،SBR ،NR و CR شده است.
الاستومرهای جدیدتر خواص شیمیایی، الکتریکی، مکانیکی، حرارتی و جوی بهبود یافته تری تولید می کنند. تنش و پیرشدن می تواند سبب ترک خوردن پوشش سیم شود. یک افزودنی خود جوش خورنده (Self-healing additive) برای پوشش سیم شامل مواد واکنشی به شکل میکروکپسولهایی است. با ایجاد ترک، میکروکپسولها مواد واکنشی را رها کرده و سیم و کابل را ترمیم می کنند.
رولیک چیست ؟
- کاربرد و مشخصات انواع قرقره های کانوایر + لیست قیمت
- محاسبه فاصله بین رولیک های رفت-برگشت و نقاط بارگیری در نقاله ها
عوامل خرابی و فاسد شدن تسمه نقاله لاستیک ها (دمای بالا)
ترکیبات و نمونه های آزمون لاستیکی به سرعت در دماهای بالا پیر می شوند و نرخ فساد و خرابی تسمه آنها افزایش می یابد، بنابراین، بایستی زمان آزمایش کوتاه شود:
دمای انتخابی به فاکتورهای مؤثر وابسته است که عبارتند از :
- قابلیت دسترسی اکسیژن
- اندازه و شکل نمونه
- وضعیت لاستیک (اشباع شده، غيراشباع)
- سرعت هوا روی سطح لاستیک در حین پیرسازی
بخاطر حضور این فاکتورها، تستها بایستی بر مبنای یک نمونه کنترل با خواص اجرایی معلوم انجام گیرد. دو نمونه تست که برای پیرسازی استفاده می شوند، 573 ASTM D و 86 ASTM D هستند. تست D573 مقاومت تخریب نمونه های مختلف ولکانیزه شده را که در هوا و در فشار اتمسفر حرارت داده میشوند باهم مقایسه می کند. خواصی که با گذر زمان تغییر می کنند نظیر: کشش و افزایش طول نسبی که تعیین می شوند. یک مشکل 573 D انتقال مواد فرار (على الخصوص، آنتی اکسیدانها) از یک نمونه ولکانیزه شده به دیگری در حین پیرسازی است.
مشکل دیگر خرابی و فاسد شدن تسمه نقاله، فقدان کنترل همه فاکتورها در حین فرآیند پیرسازی درون کوره است. کنترل سرعت هوا روی نمونه ها مهم است زیرا، آن روی ضخامت لایه مرزی هوا تأثیرگذار است و بنابراین سرعت پیرسازی را هم متأثر می کند. 865 ASTM Dاین مشکل را با پیرسازی هر نمونه در محفظه خودش حل می کند، در نتیجه، هر نمونه سیستم گردش هوایی خاص خودش را دارد و نتایج قطعی تر می تواند از تستهای جلوتر حاصل شود. که از انتقال مواد فرار از یک نمونه به دیگری جلوگیری می کند.
پایداری لاستیک شدیدا، انتخاب یک دمای شتاب دهنده تست و یک دمای معمولی برای NBR و SBR که حدود C° 100 است را تحت تأثیر قرار میدهد.
تاثیرات دمایی بر خرابی و فساد تسمه های نقاله
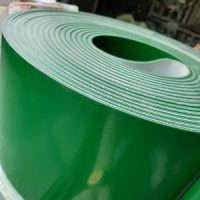
تسمه نقاله pvc
درچه مواردی از تسمه و نوار از جنس پی وی سی در کانوایر ها استفاده می شود؟
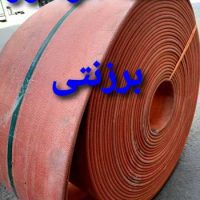
بلت الواتور برزنتی
چه موقع ازبلت های برزنتی استفاده می شود؟
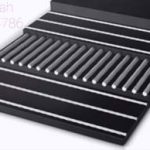
استیل کورد
چه زمانی ازتسمه نقاله با کابل های فولادی استفاده می شود؟